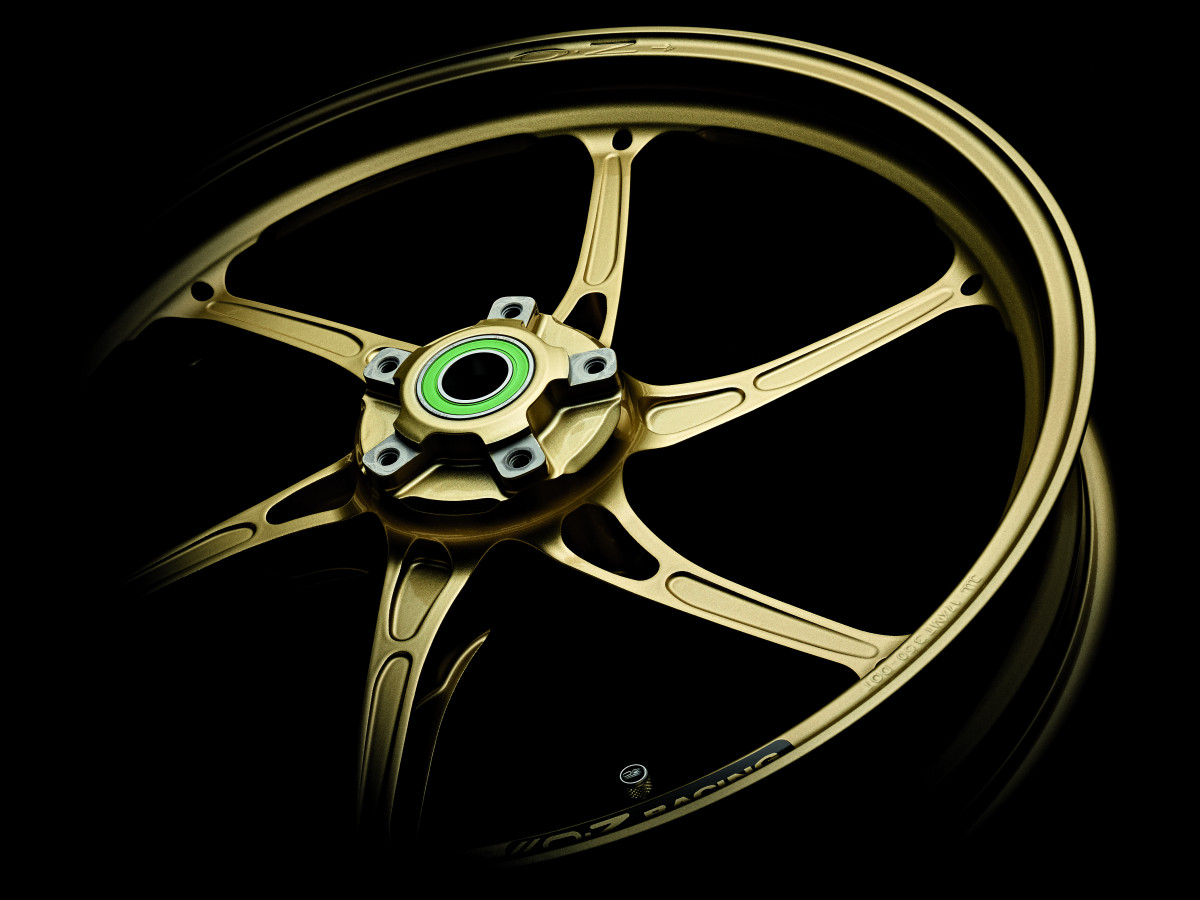
OZ Racing Wheels
OZ firmly planted its roots in the motorcycle world in the 1970s when, in its second year in business, it began to design and produce motorcycle wheels. OZ has since had a storied history in the motorcycle world as a technical partner with some of the top racing teams and manufacturers in the sport. OZ's experience at the top tier of auto racing (F1, WRC, etc.), along with its more than 40-years’ experience working with magnesium, has carried over to motorcycles and allowed them to achieve performance unanimously recognized by the top riders on circuits around the world.
Advantages of OZ Wheels
The advantages of having the lightest possible wheels on your bike cannot be overstated. OZ's combination of construction technology and material specification allows for a reduction in mass and inertia of more than 40% compared to the best stock wheels, and a savings per set of up to 9.9 lbs. (depending on the type of motorcycle).
For the rider, this translates to:
- Extraordinarily improved handling
- Greater overall performance of the motorbike in all dynamic measures
Why? Because
- The motorcycle can change direction faster
- The motorcycle will have greater speed on exiting turns
- The motorcycle can brake later
Engineering
To support its designers, OZ adopts modern computerized analysis and design systems that improve production standards and drastically reduce time-to-market. Classic CAD and CAM program are integrated by CAE (Computer Aided Engineering) stations, that can simulate the physical response of the wheel simply on the basis of its geometric model. A dedicated FEM (Finite Element Method) based software then makes it possible to optimize the geometric shape and the choice of material, to identify the product's critical factors by a virtual simulation of a physical or mechanical problem. Predictive engineering is supported by RP (Rapid Prototyping) technology, that makes it possible to create, in a very short time, physical prototypes directly from the CAD virtual model.
Testing and Quality Control
The pursuit of producing wheels of the highest quality, and providing unsurpassed customer satisfaction, remains at the center of the OZ manufacturing philosophy. Below are just some of the steps included in producing the highest quality wheels on the planet:
- Chemical analysis on raw materials and castings
- Ultrasonic Inspection to reveal defects and impurities
- Air Tightness to identify any air leaks caused by porosity (wheel submerged in a tub of water, air injected under 5-7 atm)
- Dye Penetration Inspection to identify any superficial cracks or micro-faults (chromatic contrast under UV light)
- Fatigue test wheel subjected to the same mechanical stress of a car driving along a bend
- LBF Bi-axial Wheel Testing Machine
- Rolling test simulates the behavior and reactions of the wheel along a straight stretch(maximum load, 100 km/h)
- Impact test (crash test) simulation of stresses that the wheel might suffer on the road
- Dimensional check to assess the dimensions, circularity and concentricity of the wheel (tolerances of a few tenths of mm)
- X-ray control
Raw Materials & Forging
OZ Racing wheels are born from the same raw materials that are used in the aerospace industry, where low weight and corrosion resistance are of paramount importance.
Once the ideal wheel material is chosen, it must be properly formed for ultimate strength and lightness. The mechanical and physical strength characteristics of a forged wheel are equally distributed throughout the wheel on a molecular level. The result is far greater strength than an equivalent cast wheel, vastly improving the performance of the wheel when faced with impacts and high loads.
A forged wheel is far lighter than an equivalent cast wheel. The weight reduction benefit of forged wheels serve to improve the overall performance of a vehicle by reducing the vehicle unstrung mass and improving the performance characteristics of the suspension, improving both road holding ability and dynamic cornering.
The lightweight characteristics of the forged wheel mean that it will demonstrate a lower angular momentum. In practical terms this lends an improved driving dynamic through lower power consumption during acceleration and better braking power.
When considered in application for use on motorcycles, the strength, lightness, ductility and resistance to fatigue all contribute to a reduction in the gyroscopic effect, improving braking performance.